COFA™ (COmposite Fitting Attachment) is a novel method to rapidly weld thermoplastic brackets and fittings to pre-manufactured thermoset composite panels, eliminating the need for fastening or traditional adhesive bonding.
The technique works via incorporation of a special thermoplastic polymer surfacing layer onto the surface of the thermoset composite laminates. The bracket can then be rapidly welded to the laminate using a rapid interface heating method, such as ultrasonic welding, which enables the joint to be made in a few seconds. The joints are strong enough for the requirements of many non-structural brackets, including those used within the aerospace industry.
The value of the COFA™ welding system lies in the following key benefits and advantages:
-
The rapid nature of the welding process, where joints are formed within seconds
-
The elimination of any requirement for drilling or fastening, or even surface preparation of the composite component
-
The suitability of the process for use by hand-held welders or automated systems
-
The simplicity of the welding process, with minimal or no surface preparation required
-
The possibility and ease of fitting removal and re-installation if necessary
-
The flexibility of the process to be adapted to various types of composite structures and brackets
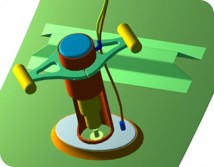